The teams at SOCOTEC drew on their expertise in technical inspections to support the project team in improving the performance of the hazard and risk prevention plan.
The aim of the Resilience project involved designing and creating a bioclimatic building in the heart of the “Ferme des Possibles” urban farm to support the activities spearheaded by the Novaedia cooperative by prioritising reused materials and maximising the use of bio-based and geo-based materials.
Key information
Project name: Resilience, La Ferme des Possibles
Date: inaugurated in September 2020
Client: Novaedia
Size: 1,882 m²
Location: Stains, Seine-Saint-Denis, France
Photo credit: Frédéric Denise architectes
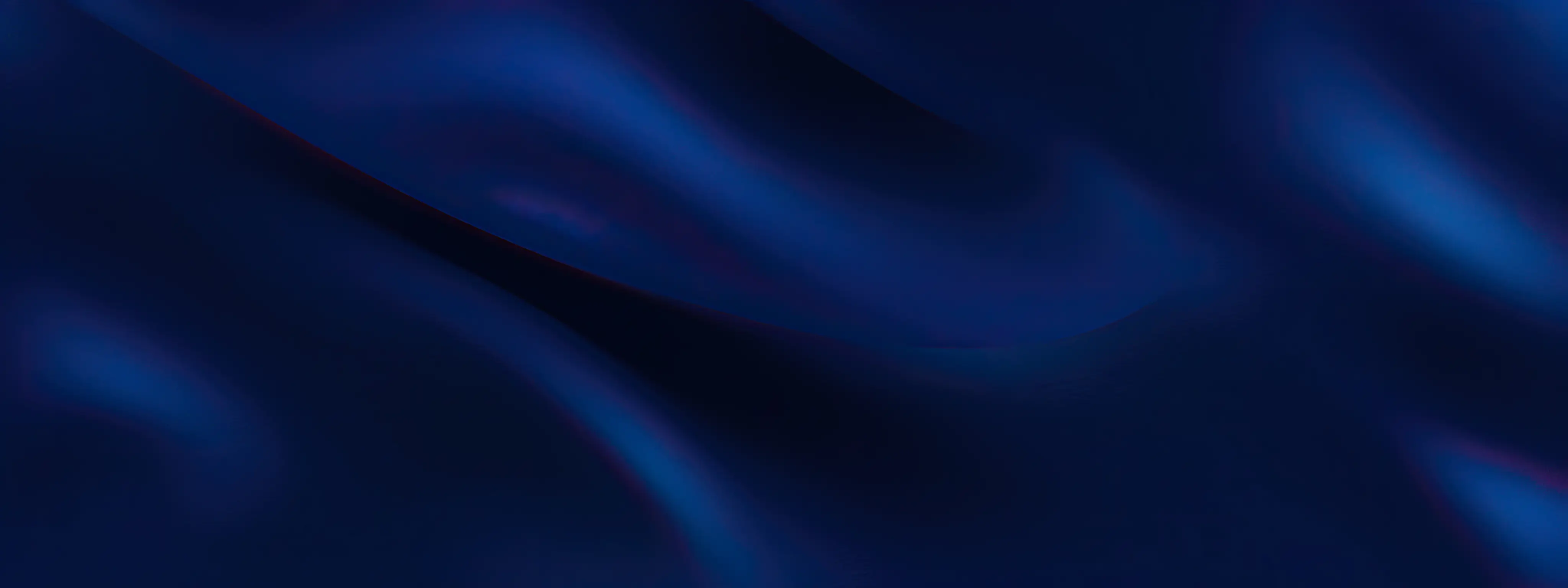
Talk to our experts
Project details
Social cooperative Novaedia was founded in the centre of Seine-Saint-Denis in 2015 with ambitions of developing an organic and supportive local food supply chain. Novaedia hires and trains around 20 people for future careers within urban agriculture, catering and logistics. The cooperative champions a socially-oriented and supportive economy that engages with the community and promotes sustainability, while striving to create new jobs and improve employability for disabled people, young people from working-class neighbourhoods and generally people struggling to find employment.
To ensure that the building reflected their values and offered a tangible example of a solution for tackling global warming, they wanted the construction to incorporate intelligent resource management practices, both in terms of its energy and its use of bio-based or reused materials. They enlisted the services of architect Frédéric Denise, whose firm specialises in buildings featuring a minimal carbon footprint.
The 1,882 m² building is entirely timber-framed. The external walls are made from a mixture of straw and earth. The internal walls have been rendered with earth from the actual site. The project team tried various types of earth until they ended up with the best result. The material is much easier to handle than plaster. It also has the advantage of being readily available, meaning that repairs can easily be made by the site’s operator.
When it came to incorporating used materials, the challenge was finding good “sources” of reusable materials. In particular, 300 identical wooden windows were salvaged from a demolished building in the area. The project had to be adapted so that they could be fitted to create a large glass façade. The windows were first prepared in the workshop before they were fitted in the timber frame. Raw earth bricks were also recovered, including all the plumbing for the sanitary facilities, radiators, glazed internal doors for the offices, double-glazed windows, acoustic panels, lampshades and paving slabs.
Description of the assignment brief
Our risk management and technical consultancy services for this ambitious project were instrumental in defining the best-fit solutions.
- Guarantee that the design and implementation processes were fully aligned with legal requirements.
- Conduct a risk assessment and propose an acceptable standard in the absence of an existing benchmark.
- Consult with the owner and contractor on the project’s insurability, so that they could communicate positively with the insurer, find solutions suiting all the parties and obtain a policy.
To learn more about Novaedia (content in French).
“This project has been a tremendous test bed for experimentation, while demonstrating the potential of reusable materials for the construction industry. One of the significant advantages has been the cost of construction, which is way below usual standards.”